

Quickcoating offers nearly unlimited application possibilities for all kinds of metal parts. Founded in 1997 501 - 1000 People 70. Industrial & Commercial Custom Powder Coating Services. Small and big series, small and big parts – this machine handles everything at minimal costs.Įven thousands of parts can be coated within shortest time and with top quality. This is approximately 1% of a basic coating chamber with exhaust and one coating gun. Nowadays more and more important: The quickcoating machine needs only ~20 W of electrical power. Some of the most common metals that undergo the powder coating process include household appliances, aluminum extrusions, drum hardware, automotive and bicycle parts. The result is a coating surface that will meet the highest quality requirements. The most common usage of powder coating is for coating metals to create a harder, tougher finish than conventional paint. This guarantees 100% powder economy.Īn expensive and cumbersome powder recovery system is not necessary.Ĭhange of colour with the new CCS-System only takes 5 minutes by exchanging the complete coating chamber.ĭue to the closed process chamber the problem of impurity and particles at the coating surface is minimized. Powder not deposited on the piece falls down to the bottom after the coating process is finished - ready to be used in the next coating cycle. In the first step, a product (usually a metal part) is cleaned and prepared for coating. Not only are you adding colour to your metal, but you are increasing its durability, receiving a. Powder coating is a multi-step finishing process. An electrostatic method is used to apply the powder coating as a dry powder, which is subsequently cured using heat. Not all materials can withstand powder coating, but most sheet metals can. The coating thickness can be adjusted between 40 and 300 µm according to the choice of coating time and charging voltage. The short answer: Powder coating offers incredible versatility. Powder coating is a dry coating procedure that is mostly used as a metal finish.

This leads to a very high electrostatic powder adhesion on the workpiece surface.
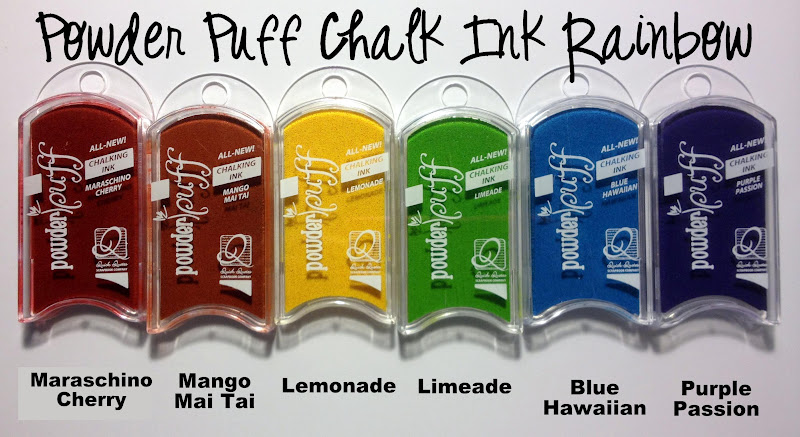
The charged powder particles now follow the electrostatic field emitted by the electrodes, thus are transported to the grounded work piece.ĭue to the quickcoating principle the powder cloud consists only of highly charged powder particles. The quickcoating technology is based exclusively upon the electrostatic powder coating principle - without the use of compressed air!Įlectrodes charge the powder particles and thus make them rise as a cloud from the bottom of the coating chamber.
